Insights
Navigating the decarbonisation challenge
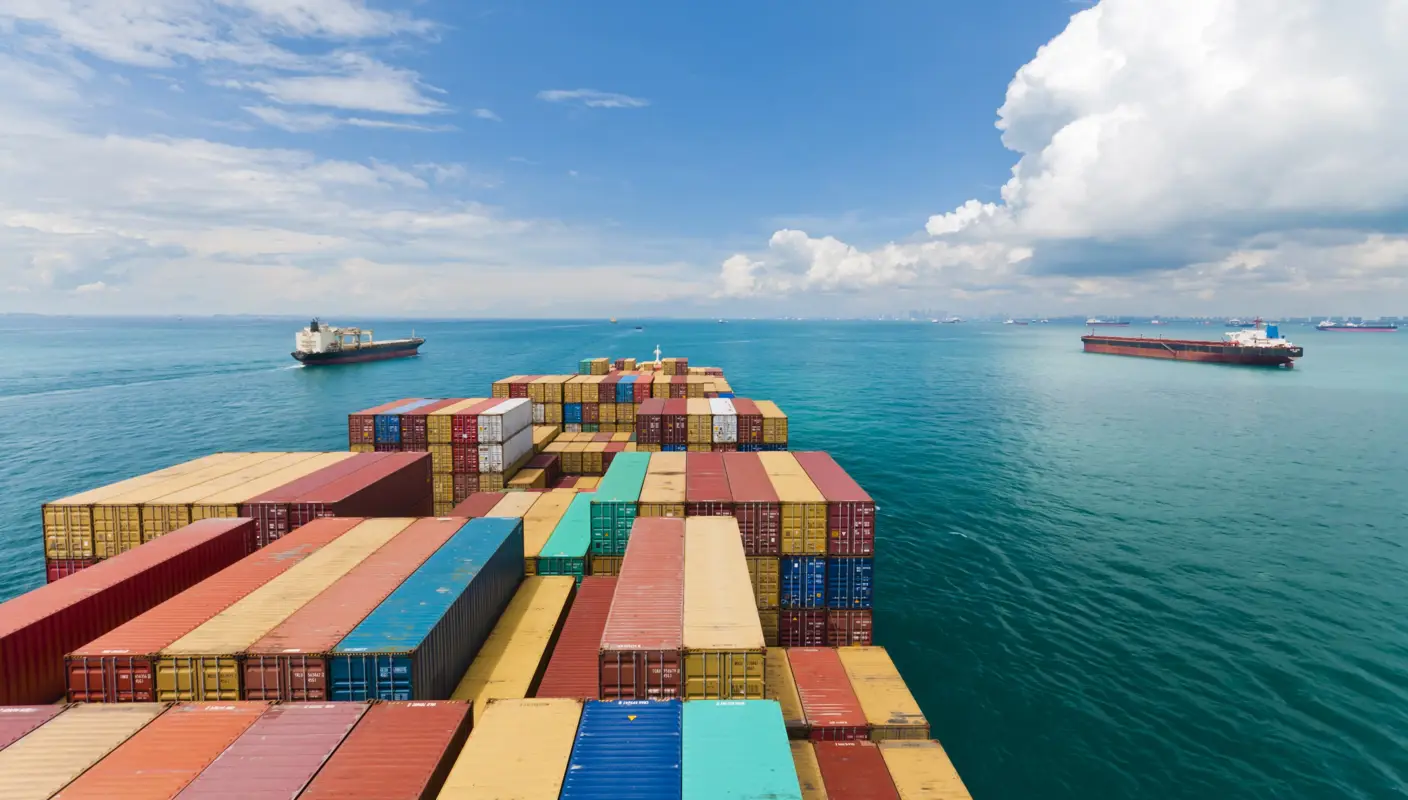
May 25, 2020
Shipping has been set a target by the International Maritime Organisation (IMO) to reduce greenhouse gas emissions by at least 50% by 2050 compared to 2008 levels. This has sparked research into a whole range of technologies including alternate fuels, vessel designs, energy saving devices, operational changes and alternatives to replace or complement conventional marine engines.
The target is currently an ambition rather than a regulation for most ship types. However, for the largest container vessels (those above 200,000dwt) it was supposed to be set in stone by changes in Energy Efficiency Design Index (EEDI) rules proposed at the Marine Environment Protection Committee (MEPC 74) meeting and due to be adopted at MEPC 75 in March/April 2020. That meeting has since been postponed because of the COVID-19 pandemic and it is not yet known when the decision will be confirmed.
Strong focus on alternative fuels
It has been two years since the IMO set its 50% by 2050 target as one milestone along the road to eventual zero emission vessels. To meet the final goal will mean that new fuels will be needed, and it has been on these that most attention has been focussed recently.
According to Alastair Marsh, CEO of classification society Lloyd’s Register, in his recent opinion piece for Asia Shipping Media, defining optimum zero-carbon fuel options will rely on an assessment of investment readiness and the dependable production of future fuels and technical readiness.
Norwegian risk management specialist DNV GL also sees decarbonisation as a major energy trend of the future. Its latest Maritime Forecast 2050 report predicts the IMO’s emissions reduction strategy will impact on costs, asset values and earning capacity more significantly than in the past. DNV GL believes that steps to the ultimate goal will mean an increasingly diverse fuel choice is needed.
Quest for greater efficiency
As important as alternative fuels are, the general consensus is that they are still several years off and even if developed earlier will not change ship operators’ constant quest for greater efficiency and reduced fuel use. There are earlier efficiency targets between now and 2050 that ships have to make to meet EEDI rules and it is already recognised that better coatings have a large role to play in that.
Indeed, the battle against hull fouling is one that has been fought almost as long as ships have existed and is still ongoing. Now that modern software tools allow the efficiency reduction of fouling to be accurately counted and with the EEDI rules requiring efficiency to be measured and rated, a functioning antifouling coating is recognised as an energy saving measure although one whose effect can be difficult to quantify, especially for operators who do not have in-house resources to conduct proper hull performance management.
Most antifouling or foul release coatings are designed for specific operational profiles taking into account average speeds, idle periods and area of operation among other factors. What works well for one operational profile will not necessarily be suitable for a ship that is operated differently.
Fouling – and consequently antifouling measures – has recently taken on fresh importance. Not only is its effect on efficiency something to be addressed but as a vector for invasive species it is even more powerful than ballast water. It is therefore expected that some international regulation may well be forthcoming in the near future to add to local regulations already in place.
Shipping turned on its head
At the end of 2019, the main topic of discussion was how the industry would cope with the reduction of the global sulphur in fuels cap from 3.5% to just 0.5% outside of ECAs. The choice for most owners was a stark one of either fitting exhaust gas cleaning systems or paying a premium of as much as $300 per tonne for compliant bunkers.
In the space of a few short weeks in mid-January, the emergence of coronavirus and the subsequent COVID-19 pandemic the anticipated future trading pattern for shipping was turned on its head. To reduce the death toll from the infection, most countries have imposed some form of lockdown choking off normal industrial, commercial and social activity. The effect has been a sudden and massive fall off in shipping demand, the halt of all cruise ships and the bizarre moment in late April when the price of crude oil reached minus $40 per barrel.
Hundreds of product and crude carriers have been taken out of normal service to act as storage for the glut of oil that has resulted from lack of demand. Container lines are cancelling sailings and deferring delivery of new ships, cruise vessels are all in temporary lay-up and the price of bunkers has fallen so low that many large ships are now finding it cheaper to sail from the Far East to Europe via South Africa rather than using Suez adding 3,500 nautical miles to the voyage with all of the extra emissions and times that involves.
All of these changes are likely to affect the efficiency of the vessels and possibly the antifouling coatings currently applied, and if they become the new normal will influence the choice of new technologies and coatings for some time to come.