Insights
Rise in offshore wind operations calls for tried and tested coatings
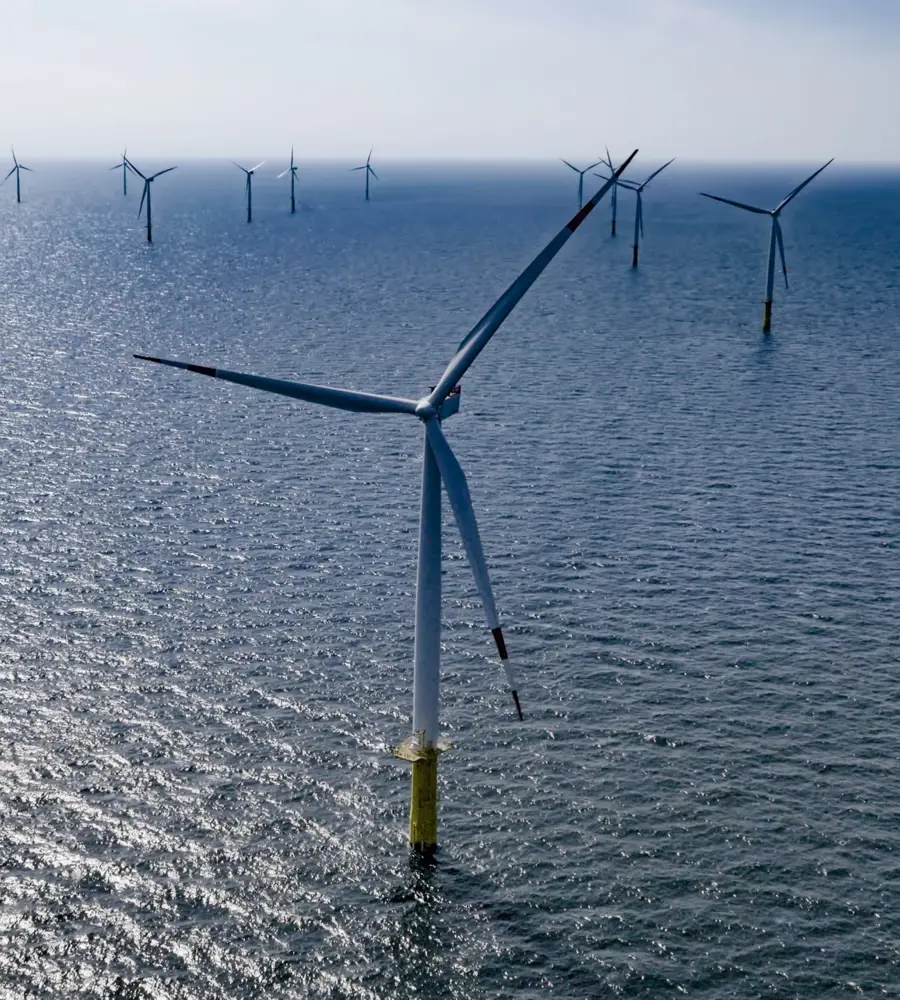
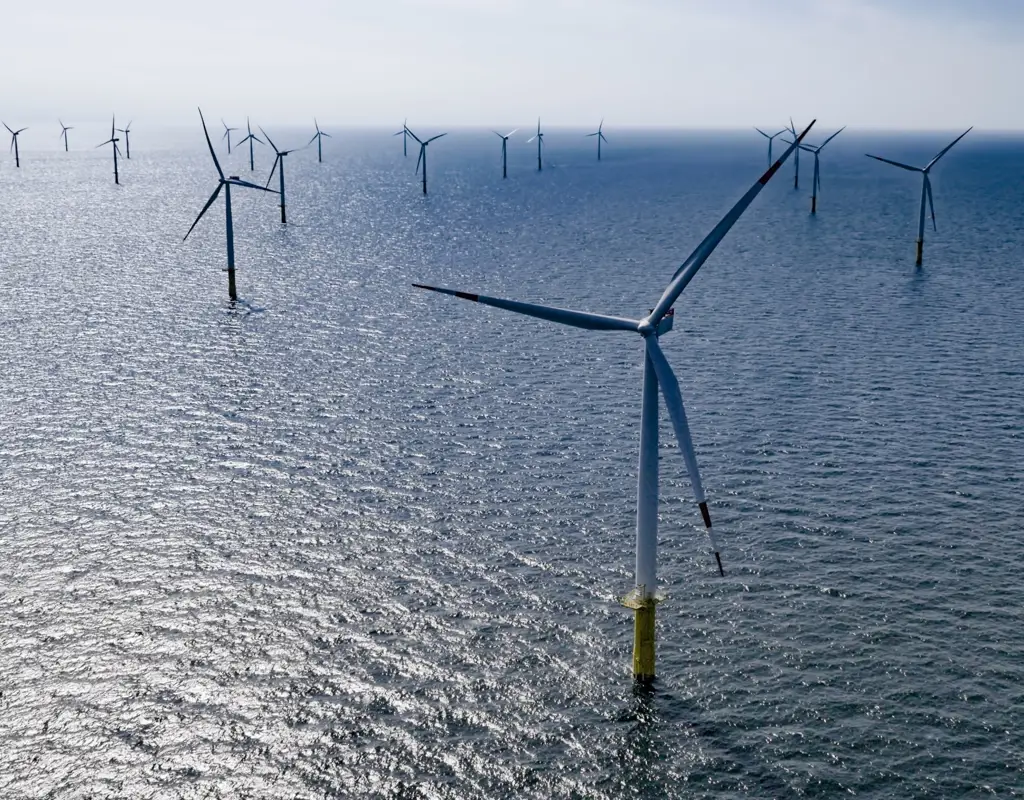
April 28, 2023
The impact of corrosion on steel cannot be overstated. The Association for Materials Protection and Performance (AMPP) has reported the cost runs into trillions of dollars with a total cost equal to 3-4% of global GDP. It also said that around 20% of the world’s annual steel production is used solely for replacing damaged and corroded steel in all of its various forms and applications. Those figures cover all applications including relatively benign environments so the impact in harsher conditions is higher.
Probably the harshest and most destructive environment imaginable for steel is at sea especially where the structure must remain in place for very long time periods extending to thirty, forty, fifty years or more. Clearly such applications need methods of keeping corrosion at bay.
Over the last half century or so, the offshore environment has become a critical source of energy. Beginning with oil and gas and more recently offshore wind, the importance of the offshore energy sector has become a vital element of infrastructure. Whilst renewable energy, epitomised by offshore wind, is considered as the future, and oil and gas are the fading stars, the offshore wind sector has much to learn from oil and gas and can benefit from decades of experience.
Operators seeking longer lifespans
“First generation offshore wind turbines have had an average life of between 20 and 25 years but to achieve economic returns, energy operators will be looking for longer lifespans to get the best returns on capital and operational expenses. Comments made by energy operators suggest that they will be looking for maintenance-free lifespans for turbine towers of somewhere between 35 and 56 years,” says Anders Skilbred, R&D Senior Chemist Technology at Jotun.
Of particular interest is the prevention of corrosion in the submerged, tidal and splash zones of offshore wind foundations. These are the areas most prone to corrosion caused by a combination of the abrasive action of waves, accumulation of salts and chemicals, mechanical impact by floating objects including maintenance vessels servicing the turbines and stress of movement of the tower.
Higher maintenance costs for offshore wind
Wind turbines may look to be much simpler structures than an oil rig but whereas an oil or gas field may be served by a handful of rigs, a typical offshore windfarm will comprise tens or hundreds of turbines. Current projections indicate 234 gigawatts of offshore wind energy will be installed globally by 2030, which could mean around 30,000 turbines. By contrast, at the end of 2021, only 201 offshore oil and gas rigs were in operation. Those figures suggest that the cost of maintenance of the turbine towers will be several orders of magnitude higher than that of oil and gas.
According to Skilbred maintenance costs for offshore wind will vary from operator to operator and reliable industry averages are as yet hard to quantify. The rule of thumb is that offshore maintenance costs are between $800 and $1,000 per m².
“Taking all of the challenges into account and not forgetting that aside from reducing maintenance costs and time lost if structures need repair or replacement, there is the environmental impact of producing the additional steel needed to give the requisite lifespans,” emphasises Skilbred.
Solutions to combat corrosion
Offshore wind structures could simply be made of thicker steel increasing the corrosion allowance but increasing wall thickness by just 1mm will add 50 tonnes of steel for the typical tower. For the expected 30,000 turbines needed by 2030 that equates to 1,500,000 tonnes of additional steel. Steel production is energy intensive and around 1.85 tonnes of CO₂ is emitted for each tonne of steel made. The steel industry is among the three biggest producers of carbon dioxide accounting for 8% of annual emissions.
Another option is to use more corrosion resistant steel alloys, but that comes with a cost not only monetary but also environmental. “Corrosion resistant alloys contain chromium, and other less abundant metals which will drive the cost and environmental footprint up. Therefore, a means of preventing corrosion could allow turbines to be made with less steel and significantly lower total CO₂ emissions due to the reduced number of maintenance cycles,” points out Skilbred.
No need to reinvent the wheel
“Unlike some of the modern technology challenges, there is no need to reinvent the wheel because, even though the offshore wind industry is relatively new, the conditions are the same as those in the oil and gas sector. So, we already have the answer that is based on decades of experience,” says Skilbred and adds, “Early jacket installations in the 1970s on the Norwegian Continental Shelf were coated with traditional epoxy coating systems. Around ten years later, glass flake reinforced polyester (GFRP) coatings appeared and these high build coatings proved much more durable. So much so that this family of high film thickness and abrasion resistant coatings were soon the preferred option for new structures and for refurbishing older structures during routine maintenance. Among the many GFRP coatings used in offshore oil and gas was Jotun’s Baltoflake.”
Proof of performance
Expanding on the history of Baltoflake, Skilbred says it was developed in the 1970s and was one of the first few performance coating products targeted for offshore environment performance. In the 1990s Jotun began producing Baltoflake Ecolife as a styrene-free alternative with exact same performance. Both products are among the top four GFRP coatings in terms of volume of paint needed to achieve an optimum protective coating and are the leading products for low VOC emissions with figures a quarter those of nearest rivals.
“Almost forty years on some of those early structures have started to be decommissioned and dismantled. Jotun has taken this unique opportunity to investigate the performance of its product by examining elements of the decommission jackets and other offshore assets. Some of the elements taken from the splash zone that were made available for testing were last coated with Baltoflake in the late 1980s and have not undergone further maintenance since that time,” explains Skilbred.
The results of the examination and analysis was presented in a paper entitled Long Term Performance of Glass Flake Reinforced Polyesters - A Case Study After 35 Years Under Offshore Conditions presented in March 2022 to the AMPP’s annual conference in San Antonio Texas, USA. The paper makes the point that visual inspection of the glass flake reinforced polyester coating revealed no significant coating degradation. And no rusting was observed.
“The tests performed on the decommissioned pieces went beyond a visual examination and used established testing procedures and advanced analysis. The results show that there was no detected under film corrosion and the adhesion values were acceptable. Further, the analysis showed that the product had undergone some ageing, however, the barrier properties of the coating system were still excellent, and it retained a similar mechanical performance to that of a newly prepared reference sample,” adds Skilbred.
From the tests performed it would be safe to assume that the coating, which had been applied under less-than-ideal service conditions as opposed to in a factory, would have continued to have provided protection against corrosion for several more years.
One very important factor to note is that the analysis of decommissioned elements demonstrates the performance of products for more than three decades under actual service conditions. Therefore, they provide considerable empirical evidence to support any claims as to performance and are more valuable than any laboratory testing can ever be.
Ensuring longevity and sustainability
“Offshore wind may be a relative newcomer but in terms of assets needing protection it will be much larger than offshore oil and gas. To ensure the longevity of offshore wind structures, a high standard of corrosion protection will be needed to reduce steel usage and maintenance time and expense,” argues Skilbred.
“Today there is a different attitude towards sustainability than there was in the 1970s and 1980s when the offshore oil and gas sector was in its infancy. Today long lifetime is all about sustainability. ESG considerations will demand less steel required, more profitable operation of renewable energy production, and lower total CO₂ emissions due to the reduced number of maintenance cycles,” opines Skilbred.
“Drawing on the experiences of oil and gas, the obvious choice for protective coating that can achieve those aims is a GRFP product,” says Skilbred and concludes, “Energy operators may have a choice of products in this area but of those few can demonstrate the level of achievement of Baltoflake and Baltoflake Ecolife which have proven track records and which have been endorsed by customers and inspection bodies over almost four decades.”