Insights
The role of the coating advisor: upholding quality standards
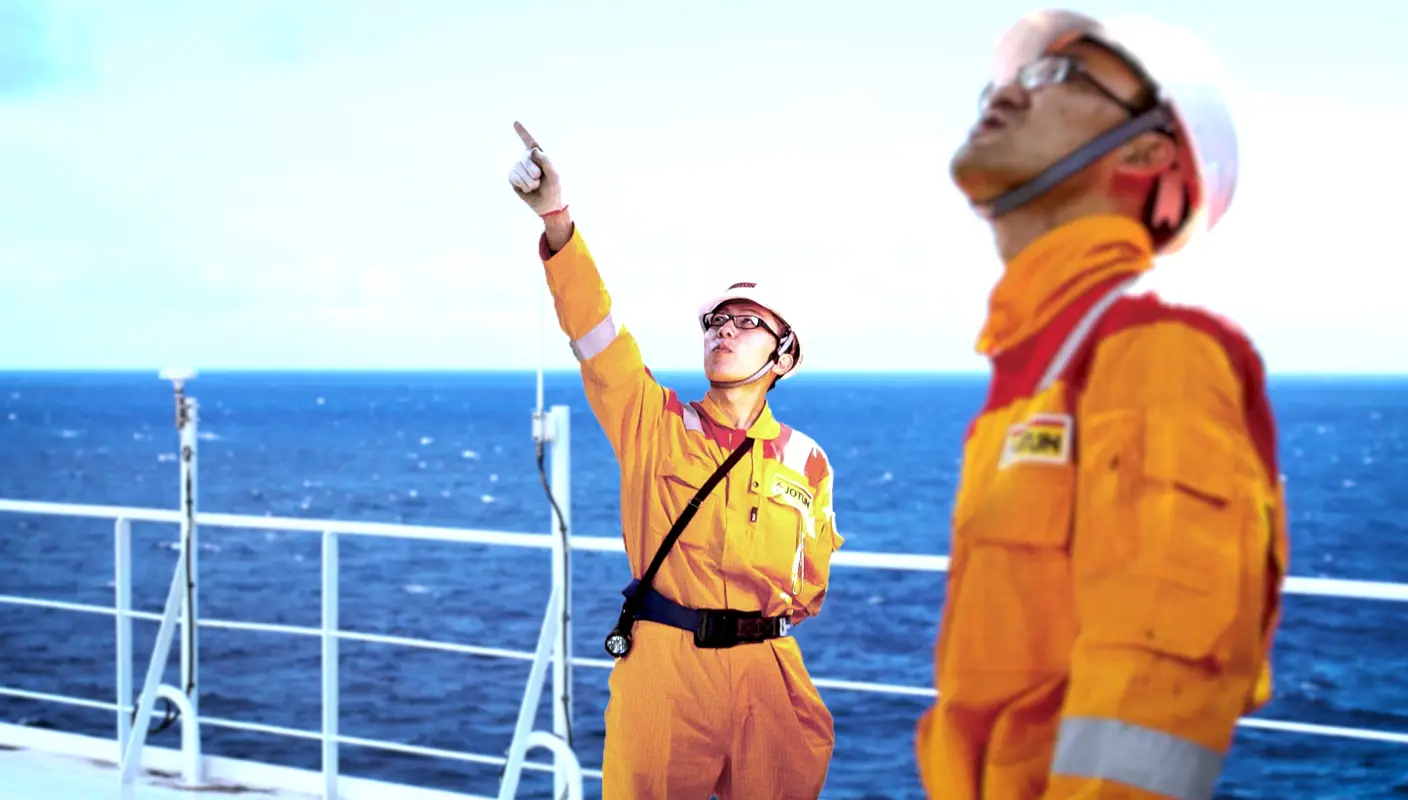
tháng 10 31, 2017
Keeping the promise of delivering a quality coating that makes a difference in improving hull performance, or corrosion protection is undoubtedly one challenge facing coating companies. A second is upholding their role as a repository of technical expertise and application guidance. This is especially important when stricter regulations on environmental performance are coming into play.
Another challenge is to channel technical expertise and competence so that it can be used as a valued resource. The market for antifouling coatings has so far been driven by a focus on cost per liter rather their effectiveness. But with the advent of advanced monitoring capabilities brought about by Big Data, much greater emphasis is being placed on the performance effects of coatings, as they come to be viewed less as a commodity and more as a technology.
Coatings Advisors, therefore, know all too well that even the best available coating, poorly applied, could have massive ramifications for ship performance. They bear the mantle of responsibility for the most vital elements of the business, and now more than ever must know their company´s products inside-out, cultivating, maintaining and updating their expertise constantly to stay ahead of the game.
"Put simply, the role of the Coating Advisor in dry docks is to deliver the project according to the agreed specification, making sure we meet customer expectations," explains Scott Petrie, global technical service manager at Jotun. "But keeping up to sped with the latest developments in hull coatings and applications, and asessing which are best for a given project is challenging. It is an extremely competitive market and all the marine coatings companies have to make sure they have qualified advisors and products that meet customer expectations and the stringent environmental regulations." Finding the balance between drydocking duration and application quality can be challenging when the forces of nature, such as precipitation, wind and temperatures, work against you. Making the right decision requires a lot of experience, understanding and skills to be provided by the coating advisor.
Expanding on the role of the coating advisor, we did a Q&A with Arul Maniam, technical service manager Jotun Singapore:
1. What is the role of the coating advisor?
Coating advisors provide professional advice to customers for the project, by proposing the best solutions and work processes involved in the application of coatings. This also involves overseeing the various steps of the painting process at the yard.
2. What do they do? What does their work entail?
- Advise yard staff on the proper application of paints to ensure coating work is carried out according to specification and procedures.
- Ensure that only valid specifications are used and adhered to, and that no shortcuts are taken in the operation
- Ensure that the specific paint type is correct and delivered in the correct quantity, in accordance with owner specifications
- Inspect equipment used for preparation and application, to ensure it is in good operational condition and that there is no risk of defects into the finished application
- Carry out inspections on the hull prior to commencement of the work to ensure surface preparation is suitable for blasting or painting works
- Provide onsite testing according to specification to ensure that the surface of the coating is finished to the best possible standard.
- Prepare detailed reports documenting work undertaken, including the results of pre- and post-application inspections and testing
3. How do they contribute to ensuring quality on the projects they are working on?
By a process of careful monitoring, inspection and close liaison with all parties concerned before, during and after application. Coating advisors ensure the successful outcome of the applied paint system.
4. What, in your opinion, are the risks/challenges, and how can they help solve them?
Now more than before, structural designs and sizes are getting more complex and bigger. A lot of thought has to be put into coating these structures
Coating advisors are constantly faced with the risks of health and safety when working onsite. Working under the hot sun or in extreme cold, they are faced with harsh environments, which make it easy to be relaxed in the face of health and safety awareness. This can lead not only to safety risks but mistakes in coating application so we constantly stress to the coating advisors to remain vigilant.
5. Are there any other aspects that you feel merit a mention?
In short, coating advisors have a difficult task - they work hard to push for the best standards in accordance with the specification, making sure it is adhered to and no shortcuts are taken in the process. But they must also make sure to balance the needs of, and maintain positive and productive relationships with the contractors, shipyards and owners. This is not necessarily recognized very often, but it is a vital aspect of the job and absolutely essential to a successful hull coating operation.